While traditional ovens have been a staple in the metal manufacturing industry for many years, rolling furnaces have raised the bar when it comes to efficiency and product quality. Let’s compare the two to help you determine which is better for your business.
1. Precision and Uniformity: Rolling Furnaces
Traditional ovens often struggle to maintain precise temperature control and even distribution of heat. In contrast, rolling furnaces excel in this aspect. They can achieve the desired temperature with remarkable accuracy and maintain uniformity throughout the entire process. This precision minimizes product inconsistencies and defects, making rolling furnaces the superior choice for businesses that prioritize quality.
2. Energy Efficiency: Rolling Furnaces
Energy consumption is a significant concern for any manufacturing operation. Traditional ovens tend to be less energy-efficient, as they often require longer heating times and higher temperatures to achieve the desired results. Rolling furnaces are designed with energy efficiency in mind, reducing operating costs and environmental impact by heating materials faster and more efficiently.
3. Flexibility and Customization: Rolling Furnaces
Rolling furnaces can be customized to suit a wide range of applications, accommodating different metal types and processing requirements. They offer greater flexibility and adaptability compared to traditional ovens, which may have limited customization options. This flexibility is a valuable asset for businesses looking to diversify their product range.
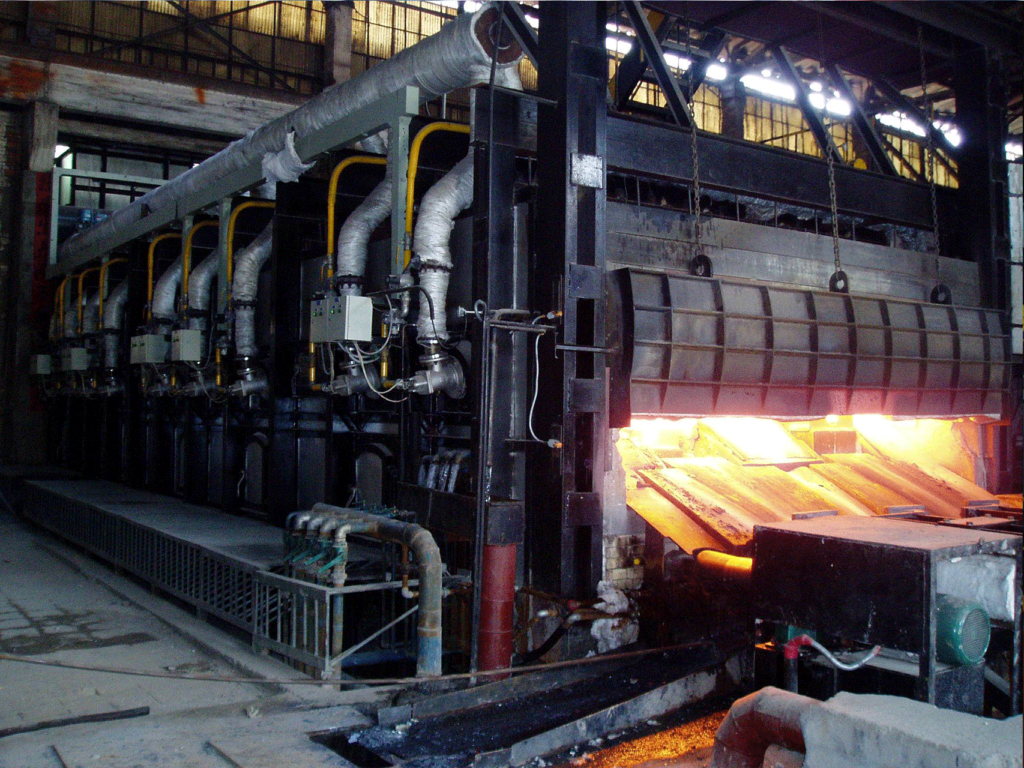
The Science Behind Rolling Furnaces: How They Work
Rolling furnaces are a key component in the metal manufacturing process, and understanding their operation is essential to grasp their significance. These furnaces are specially designed to heat and condition metal materials, making them more malleable and easy to shape during the rolling process.
The heart of a rolling furnace is its heating chamber, where temperatures can reach well over 1,000 degrees Celsius. These high temperatures are achieved through the controlled combustion of various fuels or electrical heating elements. In most cases, natural gas or electricity is used as the primary source of heat. The selection of the heat source largely depends on the specific requirements of the manufacturing process.
Once the desired temperature is reached, the metal is fed into the furnace chamber, where it undergoes a precise heating and soaking process. This critical step ensures that the metal reaches a uniform temperature throughout its entire volume, making it more pliable and easier to shape during rolling.
After the heating and soaking phase, the metal is transported to the rolling mill, where it undergoes deformation through a series of rolls. This deformation process results in the desired shape and thickness of the metal, which can then be further processed into finished products. Rolling furnaces play a crucial role in controlling the temperature and metallurgical properties of the metal during this transformation.
How Rolling Furnaces Are Redefining Efficiency in Metal Manufacturing
Rolling furnaces, like those offered by JiangSu YiNuo Thermal Energy Technology Co., Ltd., have started gaining popularity in the metal manufacturing industry, and for good reason. These advanced furnaces offer several key advantages over traditional ovens, particularly in terms of efficiency.
One of the standout features of rolling furnaces is their ability to maintain consistent and precise temperature control. This is essential in heat treatment processes, where even slight temperature variations can affect the quality of the final product. Traditional ovens may struggle to achieve and sustain the required temperatures, leading to inconsistencies in the metal’s properties. Rolling furnaces, on the other hand, offer superior control, resulting in more reliable and uniform results.
Moreover, rolling furnaces are known for their energy efficiency. Their innovative design minimizes heat loss, ultimately reducing energy consumption. This not only leads to cost savings but also contributes to a more sustainable and environmentally friendly operation, a key concern for many businesses in today’s world.
Boosting Product Quality with Rolling Furnaces: A Case Study
To truly understand the impact of rolling furnaces on product quality, let’s explore a real-world case study.
A metal manufacturing company, struggling with inconsistencies in their heat treatment process, decided to switch to rolling furnaces. The results were remarkable. The precision temperature control of rolling furnaces allowed for more even and controlled heat treatment, resulting in a significant improvement in the quality of their products.
In addition to achieving more consistent metallurgical properties, the company also experienced reduced scrap rates. Rolling furnaces helped them minimize material wastage by ensuring that fewer products ended up as rejects due to inconsistent heat treatment.
Furthermore, the rolling furnace system’s automation and remote monitoring capabilities streamlined their production process. This not only reduced labor costs but also improved overall production efficiency.
The Future of Heat Treatment: Advancements in Rolling Furnaces
The metal industry is constantly evolving, and the future of heat treatment holds exciting possibilities, many of which are driven by advancements in rolling furnaces.
One significant trend is the integration of Industry 4.0 technologies into rolling furnaces. This includes the use of sensors and data analytics to monitor and optimize the heat treatment process in real time. Companies can collect data on temperature, atmosphere, and other critical variables, allowing for proactive adjustments to ensure product consistency and quality.
Additionally, rolling furnaces are becoming more versatile, accommodating a wide range of materials and heat treatment requirements. This adaptability is particularly valuable for businesses with diverse product portfolios, as they can use a single furnace for various heat treatment processes, reducing the need for multiple specialized ovens.
Rolling furnaces manufacturers, like JiangSu YiNuo Thermal Energy Technology Co., Ltd., are also investing in research and development to improve energy efficiency further. This not only reduces operating costs but also aligns with the industry’s growing focus on sustainability and environmental responsibility.
Conclusion
In conclusion, rolling furnaces are transforming the landscape of metal manufacturing. Their ability to offer precise temperature control, energy efficiency, and improved product quality makes them a compelling alternative to traditional ovens. The case study highlighted the tangible benefits businesses can achieve by making the switch.
As advancements in rolling furnaces continue, the future of heat treatment in the metal industry looks promising, with increased automation, versatility, and sustainability at the forefront of innovation. If you’re in the metal manufacturing business, it’s worth considering how rolling furnaces from manufacturers like JiangSu YiNuo Thermal Energy Technology Co., Ltd., could revolutionize your operations and propel your business to new heights.