Reheating furnaces are an essential part of the steel manufacturing process, as they are used to heat steel ingots, billets, and other raw materials to specific temperatures, necessary for subsequent manufacturing processes. Traditional reheating furnaces are known to be energy-intensive, leading to higher operational costs and environmental concerns. However, with the latest technological advancements, innovative reheating furnaces are now available that offer consistent and precise heating results while minimizing energy consumption.reheating furnace.
One of the key features of innovative reheating furnaces is the ability to control the temperature of the furnace accurately. Modern reheating furnaces use advanced control systems that can monitor and adjust the temperature within the furnace, ensuring that the material being heated is heated to the precise temperature required. This precise temperature control not only results in better product quality but also reduces energy waste, as less energy is required to maintain the desired temperature.
Another feature of innovative reheating furnaces is their improved combustion technology. These furnaces use high-efficiency burners that can provide more complete and efficient combustion of fuel. This results in lower energy consumption, reduced emissions, and improved temperature control. Additionally, some innovative reheating furnaces use regenerative burners that can recover and reuse the waste heat generated during the heating process, further reducing energy consumption and costs.
What Is a Reheating Furnace?
A reheating furnace is a type of industrial furnace used to heat metal materials, such as steel billets, blooms, slabs, and ingots, before hot working or further processing. The purpose of a reheating furnace is to raise the temperature of the metal material to a specific temperature that is optimal for the subsequent manufacturing process.
Reheating furnaces typically use fuels such as natural gas, coal, or oil to generate heat, which is then transferred to the metal material through convection or radiation. There are different types of reheating furnaces available, including walking beam furnaces, pusher furnaces, rotary hearth furnaces, and more, each with unique advantages and applications.
The efficiency of a reheating furnace is crucial for the overall efficiency of the manufacturing process, as it affects both energy consumption and productivity. Therefore, modern reheating furnaces incorporate advanced technologies and control systems to optimize their performance and minimize waste.
How Does Reheating Furnace Work?
Reheating furnaces are an important component of the steel manufacturing process, used to heat metal materials, such as steel billets, slabs, and ingots, to a specific temperature before they are subjected to further processing. The way a reheating furnace works depends on its type, but they all follow similar basic principles.
The reheating process starts with charging the raw material onto a roller table, which feeds it into the furnace. Once inside the furnace, the material is exposed to high temperatures generated by burners or heating elements. The heat is transferred to the material through convection, radiation, or a combination of both, depending on the type of furnace.
To maintain the desired temperature, the furnace is equipped with sophisticated control systems that regulate the burners, fuel flow, and air supply. This ensures that the temperature is consistent and accurate throughout the entire heating process, which is crucial for obtaining the desired physical properties of the material.
Once the material has reached the required temperature, it is discharged from the furnace and transferred to the next stage of the manufacturing process, such as rolling or forging. The discharge process is usually automated, using a mechanism such as a walking beam, pusher, or roller table, depending on the type of furnace.
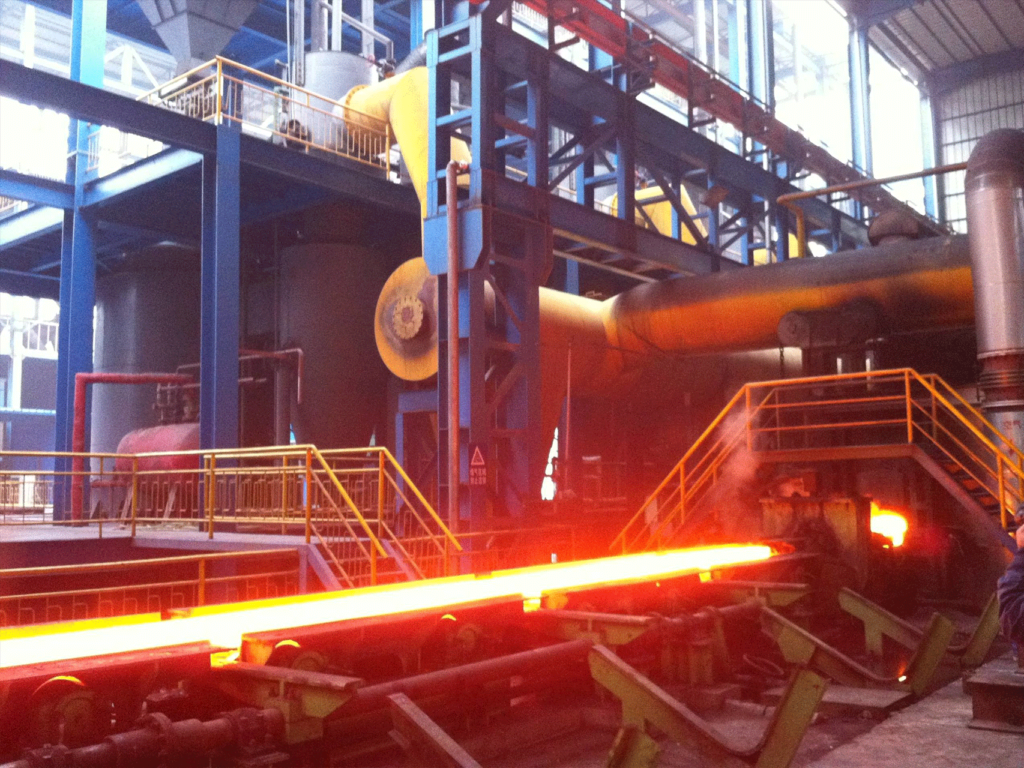
Applications of Reheating Furnace
Reheating furnaces are widely used in the steel and metalworking industries for a variety of applications. Some of the key applications of reheating furnaces include:
- Steel production: Reheating furnaces are used to heat steel billets, slabs, and ingots to a specific temperature, making them easier to shape or process. The reheated steel can then be rolled, forged, or formed into the desired shape.
2) Aluminum production: Reheating furnaces are used in the aluminum industry to heat aluminum ingots or scrap material before they are processed further. The reheating process helps to reduce the viscosity of the aluminum, making it easier to shape.
3) Heat treatment: Reheating furnaces are used in the heat treatment of steel and other metals. The heating process can change the physical and chemical properties of the material, making it stronger, more durable, or more resistant to corrosion.
4) Forging: Reheating furnaces are used in forging operations to heat the metal to a specific temperature before it is shaped or formed. The reheating process makes the metal more malleable, allowing it to be forged into complex shapes.
5) Annealing: Reheating furnaces are used in the annealing process, which involves heating the metal to a specific temperature and then allowing it to cool slowly. Annealing can improve the ductility, toughness, and machinability of the material.
6) Rolling: Reheating furnaces are used in the rolling process to heat the steel to a specific temperature before it is passed through a series of rollers to reduce its thickness.
7) Extrusion: Reheating furnaces are used in the extrusion process to heat the metal to a specific temperature before it is forced through a die to produce a specific shape.
Enhance Your Steel Processing Operations with Customizable Reheating Furnace Solutions
JiangSu YiNuo Thermal Energy Technology Co., Ltd. is a leading provider of customizable reheating furnace solutions for the steel and metalworking industries. With over 20 years of experience, they have developed a reputation for delivering high-quality, reliable, and energy-efficient reheating furnaces that meet the unique needs of their customers.
One of the key advantages of working with JiangSu YiNuo Thermal Energy Technology Co., Ltd. is their ability to customize their reheating furnace solutions to meet the specific needs of their customers. They offer a range of furnace designs, including walking beam furnaces, pusher furnaces, and rotary hearth furnaces, that can be tailored to fit the size, shape, and throughput requirements of each customer.
Their reheating furnaces are equipped with advanced control systems that provide precise temperature control, ensuring consistent and accurate heating results. They also use high-efficiency burners that minimize fuel consumption and reduce emissions, making their furnaces more sustainable and cost-effective.
Bottom Line
JiangSu YiNuo Thermal Energy Technology Co., Ltd. offers customizable reheating furnace solutions that can enhance steel processing operations by providing precise temperature control, high efficiency, and reliable performance. Their commitment to customization, sustainability, and customer service has earned them a reputation as a leading provider of reheating furnace solutions in the industry.