Metalworking and forging require the utilization of preheating furnaces for successful and accurate production. These heated chambers, crafted to heat metals to exact temperatures ahead of further shaping or treatment, are key for manufacturing goods with premium quality as well as reducing materials misuse. In this blog, let’s explore deeper into preheating furnaces, from their applications and industry trends to upkeep instructions & more. As a bonus, learn about JiangSu YiNuo Thermal Energy Technology Co., Ltd., a leading producer of this type of product.
Understanding Preheating Furnaces:
1.1 Overview and Function:
Preheating furnaces are used to elevate the temperature of metals, enhancing their malleability, reducing internal stresses, and improving their response to subsequent manufacturing processes. By bringing the metal to a precise temperature range, preheating furnaces facilitate easier deformation, reduce the risk of cracking or fracturing, and enable precise shaping and forming.
1.2 Applications and Case Studies:
Preheating furnaces find extensive applications in diverse industries, including automotive, aerospace, construction, and heavy machinery. Custom-designed preheating furnace projects cater to specific applications, such as forging, welding, heat treatment, and stress relieving. For example, in the automotive industry, preheating furnaces are crucial for forming and shaping components like crankshafts, connecting rods, and camshafts, ensuring optimal strength and durability.
Industry Trends and Innovations:
2.1 Advanced Heating Technologies:
The metalworking and forging industry continuously seeks innovative solutions to enhance efficiency and productivity. Advancements in heating technologies, such as induction heating, electric resistance heating, and gas-fired furnaces, have improved the accuracy, speed, and energy efficiency of preheating processes. These technologies offer precise temperature control, rapid heating rates, and reduced energy consumption, resulting in cost savings and improved environmental sustainability.
2.2 Integration of Automation and Data Analytics:
The integration of automation and data analytics in preheating furnace systems has revolutionized process control and optimization. Smart furnaces equipped with sensors, actuators, and advanced control algorithms enable real-time monitoring, adaptive heating profiles, and predictive maintenance. These capabilities not only improve productivity but also ensure consistent quality, minimize downtime, and enhance worker safety.
Best Practices for Preheating Furnaces:
3.1 Optimal Furnace Design:
The design of preheating furnaces should consider factors such as material type, size, and heating requirements. Adequate insulation, efficient heat transfer mechanisms, and well-designed airflow patterns are essential for achieving uniform heating and minimizing heat loss. Customization options offered by manufacturers like JiangSu YiNuo Thermal Energy Technology Co., Ltd. allow tailored furnace solutions to meet specific process demands.
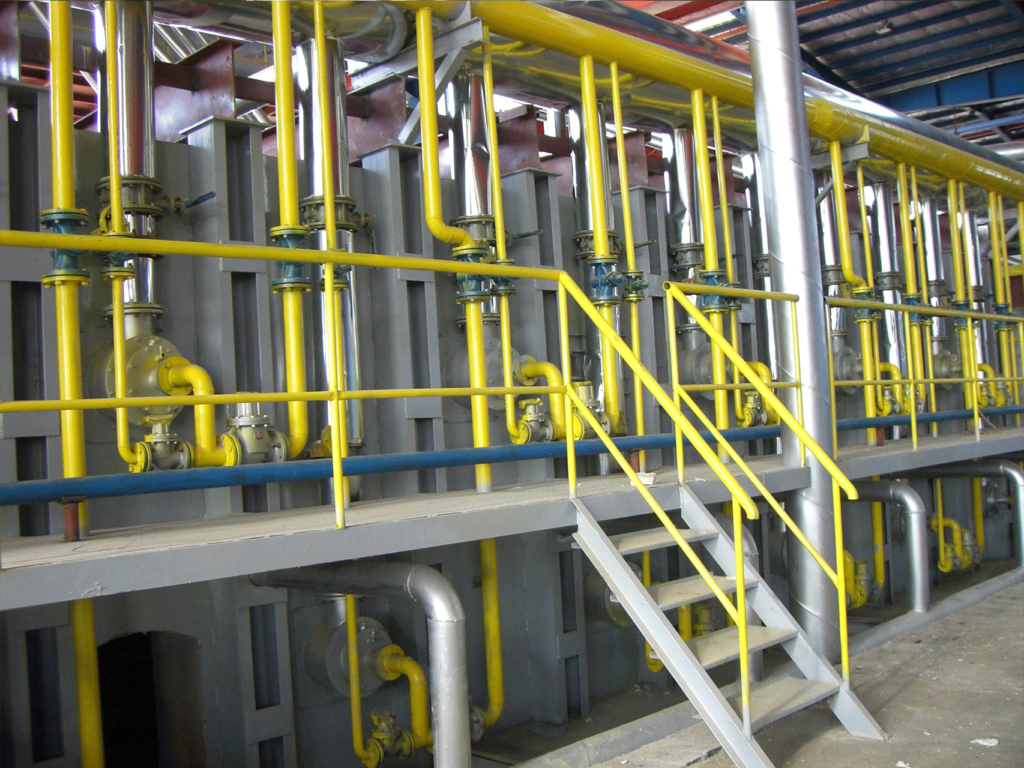
3.2 Energy Efficiency Measures:
To minimize energy consumption and operational costs, it is crucial to implement energy-efficient practices. This includes optimizing furnace insulation, implementing heat recovery systems, and employing advanced combustion technologies. Regular maintenance, including cleaning and calibration, also ensures efficient operation and extends the lifespan of the furnace.
Safety Guidelines and Compliance Standards:
4.1 Workplace Safety:
Operating preheating furnaces requires adherence to strict safety guidelines to prevent accidents and protect personnel. These guidelines encompass proper handling of hot metals, personal protective equipment (PPE), and emergency response procedures. Comprehensive training programs should be provided to employees to ensure their safety and foster a culture of awareness and responsibility.
4.2 Compliance Standards:
Preheating furnace operations must comply with industry-specific safety standards, such as those set by organizations like the Occupational Safety and Health Administration (OSHA) or the International Organization for Standardization (ISO). Regular inspections, maintenance, and documentation of safety protocols are essential to meet regulatory requirements and ensure a safe working environment.
Maintenance and Troubleshooting:
5.1 Regular Inspections and Maintenance:
Routine inspections and maintenance are critical for the optimal performance and longevity of preheating furnaces. This includes checking for wear and tear, cleaning heating elements, replacing damaged components, and verifying temperature accuracy. By conducting proactive maintenance, potential issues can be identified early on, minimizing downtime and preventing costly repairs.
5.2 Troubleshooting and Diagnostic Techniques:
In the event of furnace malfunctions or performance issues, troubleshooting becomes essential. Common problems may include uneven heating, temperature deviations, or burner inefficiencies. Utilizing diagnostic techniques, such as thermocouple calibration, electrical testing, and airflow analysis, can help identify and resolve these issues effectively, ensuring uninterrupted production and consistent product quality.
Preheating Furnace: Customized Solutions Tailored to Your Requirements
6.1 High-Temperature Preheating Furnaces:
JiangSu YiNuo Thermal Energy Technology Co., Ltd. specializes in the design and manufacturing of high-temperature preheating furnaces that can reach and maintain extreme temperatures required for various metalworking and forging applications. These furnaces are equipped with advanced heating elements and insulation materials to ensure optimum heat transfer and energy efficiency.
6.2 Customizable Furnace Sizes and Configurations:
Understanding that different industries have unique requirements, JiangSu YiNuo Thermal Energy Technology Co., Ltd. offers a wide range of customizable furnace sizes and configurations. Whether you need a small-scale furnace for intricate metal components or a large-scale furnace for heavy-duty industrial applications, they can tailor their solutions to match your specific needs.
Advanced Features and Technologies
7.1 Temperature Control and Uniformity:
JiangSu YiNuo Thermal Energy Technology Co., Ltd. integrates state-of-the-art temperature control systems into their preheating furnaces, ensuring precise and uniform heat distribution throughout the chamber. This feature allows for consistent heating of metal components, minimizing the risk of thermal gradients and ensuring superior product quality.
7.2 Energy Efficiency and Cost Savings:
Efficiency and sustainability are key considerations in modern manufacturing processes. JiangSu YiNuo Thermal Energy Technology Co., Ltd. employs innovative technologies and insulation materials to maximize energy efficiency in their preheating furnaces. This not only reduces operating costs but also contributes to a greener and more environmentally friendly production environment.
Conclusion:
Preheating furnaces are indispensable tools in the metalworking and forging industry, enabling precise shaping, enhancing material properties, and ensuring high-quality end products. By leveraging advanced technologies, adhering to best practices, and prioritizing safety and compliance, manufacturers can optimize their furnace performance, achieve energy efficiency, and elevate overall productivity. Companies like JiangSu YiNuo Thermal Energy Technology Co., Ltd. provide customized preheating furnace solutions and expertise to meet the evolving demands of the industry, enabling manufacturers to excel in their metalworking and forging endeavors.