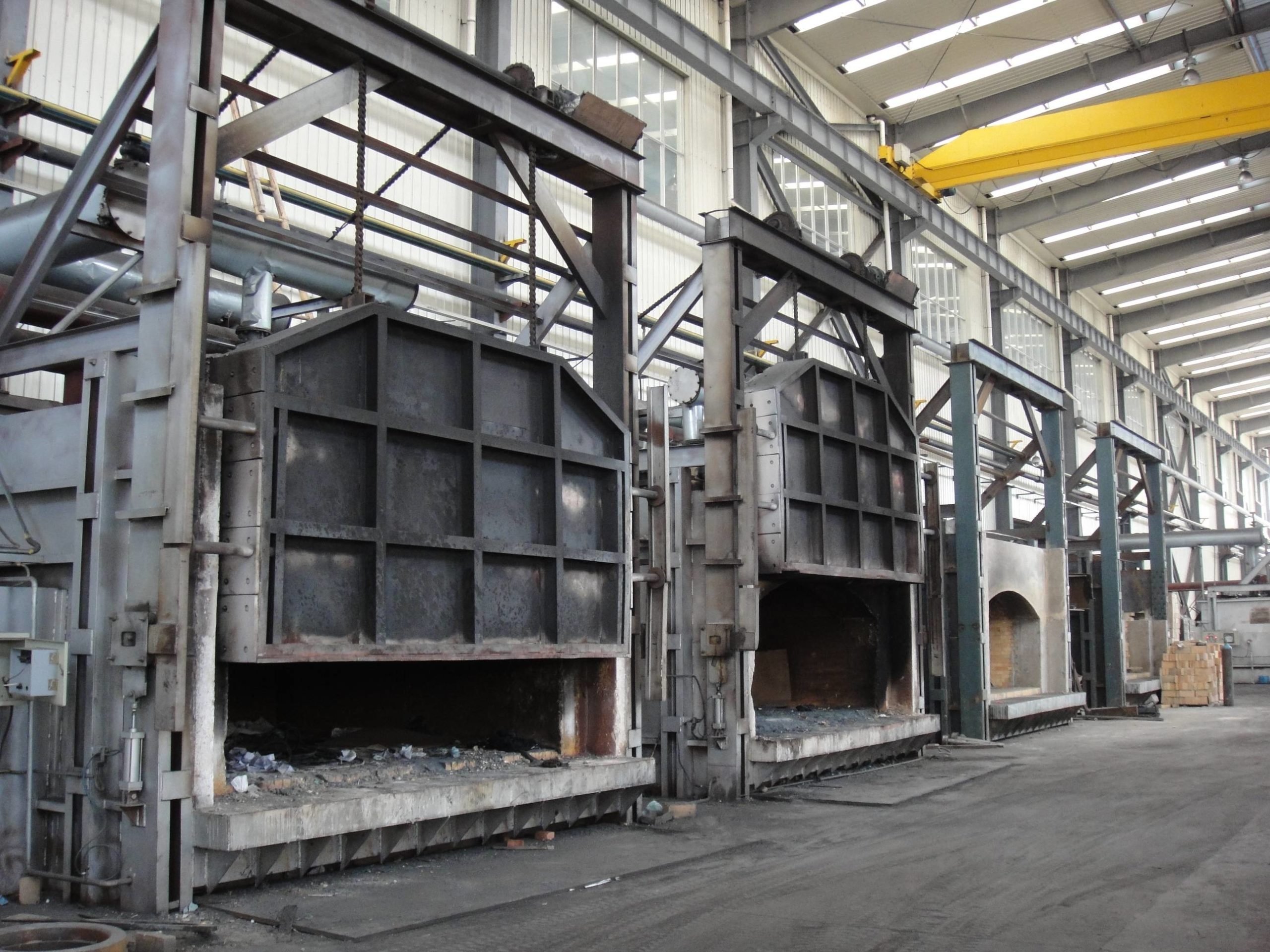
Continuous heat treatment furnaces are used in industries that require high-temperature processing of materials. These furnaces provide a continuous flow of heat to materials, ensuring a consistent and even temperature distribution throughout the entire process. Jiangsu YiNuo Thermal Energy Technology Co., Ltd., is one manufacturer of these furnaces; it has been providing high-quality thermal energy solutions to customers worldwide.
Precision is Key: Why Precise Temperature Control is Crucial in Continuous Heat Treatment Furnaces
To understand the importance of continuous heat treatment furnaces, it is essential to consider the requirements of various industries that use these furnaces. For example, in the aerospace industry, materials must be treated at specific temperatures to ensure their structural integrity and resistance to high-pressure and high-temperature environments. Similarly, in the automotive industry, heat treatment is necessary to improve the durability and strength of engine components.
One of the key requirements for continuous heat treatment furnaces is precise temperature control. The temperature must be maintained within a narrow range to ensure consistent product quality and to avoid damage to the materials being processed. Furnaces that are unable to maintain precise temperature control can result in product defects, increased material waste, and decreased productivity.
Another important requirement for continuous heat treatment furnaces is the ability to operate continuously for extended periods. Some processes can take several hours or even days to complete, and interruptions in the heating process can cause significant delays and impact the quality of the final product. Therefore, continuous heat treatment furnaces must be designed to operate efficiently and reliably over extended periods, minimizing downtime and maximizing productivity.
Power of Continuous Heat Treatment Furnaces in Meeting Industry Standards and Customer Demands
Continuous heat treatment furnaces have become increasingly popular in meeting industry standards and customer demands consistency and quality. These furnaces are designed to provide continuous heating of metal bars or other materials, allowing for a consistent temperature and high-quality production.
JiangSu YiNuo Thermal Energy Technology Co., Ltd. is one manufacturer of continuous heat treatment furnaces that have been successful in meeting the needs of customers across a range of industries. They have developed a range of furnaces that use gas-fired burners, electric heating elements, or induction heating to maintain a constant temperature and ensure the highest level of consistency in the production process.
JiangSu YiNuo Thermal Energy Technology Co., Ltd. has a range of continuous heat treatment furnaces that can be customized to meet the specific needs of their customers. Their furnaces are designed to meet industry standards and ensure high-quality production, while also providing the efficiency and cost savings that customers demand.
Revolutionizing Heat Treatment Processes: The Advantages of Continuous Furnace
Heat treatment is a critical process in the manufacturing of metal products. It involves heating and cooling metal to change its properties and improve its performance. The traditional batch furnace method of heat treatment has limitations in terms of productivity and efficiency. However, with the advent of continuous furnaces, the heat treatment process has been revolutionized.
Continuous furnaces, such as those designed by JiangSu YiNuo Thermal Energy Technology Co., Ltd., offer several advantages over batch furnaces. They are specifically designed for high-temperature metalworking processes such as forging, extrusion, and rolling. Here are some of the key features that make continuous furnaces an ideal solution for these applications.
1. Continuous Operation:
Continuous furnaces operate continuously, allowing for a constant flow of workpieces through the furnace. This feature increases productivity and efficiency, as there are no downtime and waiting periods for heating and cooling cycles.
2. Temperature Control:
Continuous furnaces are designed to maintain a consistent and precise temperature throughout the heating zone. This ensures that the workpieces are heated uniformly and to the desired temperature. Precise temperature control is critical in achieving the desired material properties, reducing the risk of product defects.
3. Energy Efficiency:
Continuous furnaces are designed to minimize heat loss and maximize energy efficiency. They are equipped with insulation to reduce heat loss and are often designed with a regenerative burner system that recovers and reuses waste heat. This feature helps reduce energy consumption, lower operating costs, and minimize environmental impact.
4. High Throughput:
Continuous furnaces can handle large volumes of workpieces, making them ideal for high-volume production runs. They can be customized with multiple heating zones and loading and unloading systems to optimize their performance, enabling manufacturers to produce high-quality products efficiently.
5. Customizable:
Continuous furnaces can be customized to meet the specific needs of different metalworking applications. Manufacturers can tailor the furnace’s features and functionality to their unique requirements, ensuring optimal performance and efficiency.
Continuous Heat Treatment Furnaces vs Batch
Continuous heat treatment furnaces and batch furnaces are both commonly used in the manufacturing industry to heat treat materials such as metal bars, rods, or tubes. Each type of furnace has its advantages and disadvantages, and choosing the right one for your operation will depend on several factors.
Continuous heat treatment furnaces, also known as continuous annealing furnaces, are designed to heat materials continuously rather than in batches. These furnaces are generally long, narrow chambers that are lined with heat-resistant materials and equipped with heating elements. The material to be heat-treated is fed into one end of the furnace and moves through the chamber on a conveyor system or other mechanism while being heated to a specific temperature.
On the other hand, batch furnaces are designed to heat materials in batches rather than continuously. These furnaces are typically smaller and less expensive than continuous heat treatment furnaces, and they are ideal for smaller-scale operations. In a batch furnace, a specific amount of material is loaded into the furnace and heated to the desired temperature. Once the material has been heated, it is removed from the furnace and replaced with a new batch.
When choosing between continuous heat treatment furnaces and batch furnaces, manufacturers must consider the specific needs of their operation. For high-volume production runs of simple parts, continuous heat treatment furnaces are likely the best option. However, for smaller-scale operations or complex heat-treatment processes, batch furnaces may be more suitable.
Conclusion
Continuous heat treatment furnaces are essential tools for various industries that require high-temperature processing of materials. These furnaces must meet strict requirements for precise temperature control, reliability, and efficiency to ensure consistent product quality and maximum productivity. JiangSu YiNuo Thermal Energy Technology Co., Ltd. is a trusted manufacturer of these furnaces, providing customized solutions that meet the unique needs of each customer.