Regenerative Burner Reheating Furnace is a cutting-edge industrial heating system that utilizes a regenerative burner combustion system to achieve remarkable energy efficiency. By recovering and reusing heat generated during the combustion process, this innovative furnace offers significant advantages over traditional heating systems. In this blog, we will delve into the features, working principles, and characteristics of the regenerative burner reheating furnace, highlighting its potential to revolutionize various industrial applications.
Features of Regenerative Burner Reheating Furnace: Regenerative Burner Combustion System
The regenerative burner reheating furnace employs a regenerative burner combustion system, which comprises the following features:
- Burner Type: The system utilizes a pair of burners that alternate between firing and preheating functions. This unique configuration optimizes heat transfer and energy efficiency.
2. Fuel Type: The regenerative burner reheating furnace can operate on a variety of fuels, including natural gas, propane, diesel, and more. This flexibility allows for adaptability to different fuel availability and cost considerations.
3. Heat Exchanger Type: The heat exchanger in this furnace is typically constructed using ceramic, metallic, or refractory materials. These materials are selected for their excellent heat retention properties, ensuring efficient heat transfer and storage.
4. Temperature Range: The regenerative burner reheating furnace can achieve high temperatures ranging from 900 to 1800 degrees Celsius, depending on the specific application requirements. This capability makes it suitable for a wide range of industrial processes.
5. Heating Capacity: The heating capacity of the furnace can be customized based on the size and configuration of the system. It can range from a few hundred thousand BTUs per hour to several million BTUs per hour, enabling it to cater to diverse industrial needs.
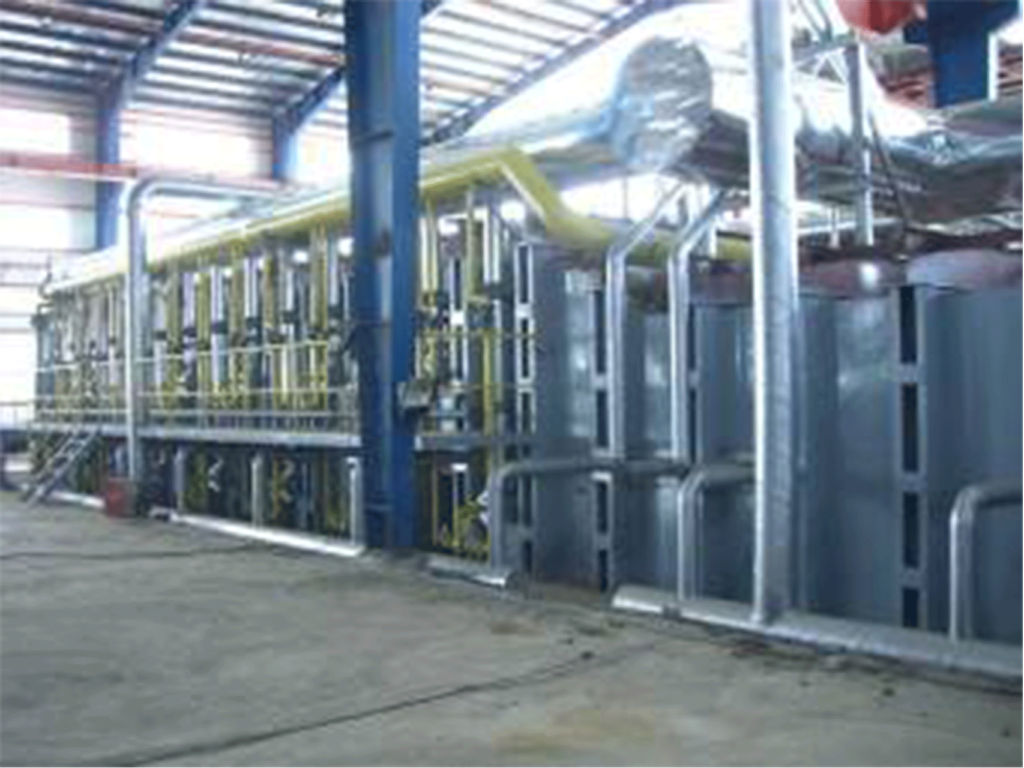
Choosing the Right Regenerative Burner Reheating Furnace:
1. Understanding Heating Requirements:
When selecting a regenerative burner reheating furnace, it is crucial to assess your specific heating requirements. Consider factors such as the desired temperature range, heating capacity, and the type of material being heated. By understanding these requirements, you can choose a furnace that matches your production needs while optimizing energy efficiency.
2. Efficiency and Fuel Consumption:
Energy efficiency is a key consideration for any industrial furnace. Look for regenerative burner reheating furnaces that are designed to maximize heat recovery and minimize fuel consumption. High-efficiency burners and advanced heat exchange systems can significantly reduce operational costs while minimizing environmental impact.
3. Temperature Control and Uniformity:
For precise and uniform heating, it is essential to select a regenerative burner reheating furnace that offers excellent temperature control capabilities. Look for features such as multiple temperature zones, advanced control systems, and precise monitoring instruments. This ensures consistent heat distribution throughout the heating chamber, enhancing the quality of the end product.
4. Safety Features and Compliance:
Safety is paramount when operating any industrial furnace. Ensure that the regenerative burner reheating furnace complies with relevant safety standards and regulations. Look for features such as flame monitoring and automatic shutdown systems to mitigate potential hazards. Additionally, consider the availability of emergency backup systems and comprehensive training for personnel.
Maintaining a Regenerative Burner Reheating Furnace:
1. Regular Cleaning and Inspection:
Regular cleaning and inspection are vital for maintaining optimal performance and prolonging the lifespan of the regenerative burner reheating furnace. Clean the burner, combustion chamber, and heat exchangers to remove any debris or carbon deposits. Inspect for signs of wear, corrosion, or leakage, and address any issues promptly.
2. Proper Lubrication and Component Maintenance:
Ensure that all moving parts, such as fans and blowers, are properly lubricated as per the manufacturer’s recommendations. Regularly inspect and maintain seals, gaskets, and other critical components to prevent air and heat leakage. Follow the manufacturer’s guidelines for routine maintenance tasks to keep the furnace running smoothly.
3. Calibration and Control System Updates:
Periodically calibrate temperature sensors, pressure gauges, and other control system components to maintain accuracy and reliability. Stay updated with the manufacturer’s recommendations regarding control system updates or software upgrades. This ensures optimal furnace performance and minimizes the risk of operational issues.
4. Staff Training and Safety Procedures:
Train personnel on the proper operation and maintenance of the regenerative burner reheating furnace. Emphasize safety procedures and ensure that employees understand the potential risks associated with the equipment. Regularly conduct refresher courses and provide updated documentation to keep the workforce well-informed and promote a safe working environment.
Manufacturer: JiangSu YiNuo Thermal Energy Technology Co., Ltd.
One prominent manufacturer of regenerative burner reheating furnaces is JiangSu YiNuo Thermal Energy Technology Co., Ltd. With their expertise and experience, they have been at the forefront of developing advanced thermal energy solutions. Their regenerative burner reheating furnaces showcase cutting-edge technology, superior performance, and robust construction. JiangSu YiNuo Thermal Energy Technology Co., Ltd. is dedicated to providing energy-efficient and environmentally friendly solutions to industries worldwide.
Characteristics of Regenerative Burner Reheating Furnace
The regenerative burner reheating furnace boasts several noteworthy characteristics:
- High Energy Efficiency: By recovering and reusing heat, this furnace achieves significantly higher energy efficiency compared to traditional combustion systems. It helps industrial facilities reduce energy consumption and lower operational costs.
2. Reduced Emissions: The efficient combustion process and use of preheated air contribute to lower emissions of carbon dioxide, nitrogen oxides, and particulate matter. The regenerative burner reheating furnace helps businesses meet environmental regulations and enhance sustainability.
3. Improved Product Quality: The precise temperature control and uniform heating offered by this furnace result in improved product quality and consistency. It ensures that industrial processes, such as melting, annealing, or sintering, achieve optimal results.
Conclusion:
Selecting the right regenerative burner reheating furnace requires careful consideration of heating requirements, efficiency, temperature control, and safety features. Regular maintenance and adherence to manufacturer guidelines are crucial to ensure the optimal performance and longevity of the furnace. By following these tips, industrial operators can choose and maintain a regenerative burner reheating furnace that not only meets their production needs but also maximizes energy efficiency and safety.